Испытание узлов и агрегатов https://deceng.ru/uslugi/ispyitaniya-uzlov-i-agregatov — ключевой этап в обеспечении надёжности оборудования. Эти тесты позволяют выявить потенциальные дефекты, проверить соответствие требованиям и продлить срок службы устройства. Процесс включает этапы проверки отдельных компонентов и их взаимодействия в системе, что критично для сложных механизмов, применяемых в различных отраслях.
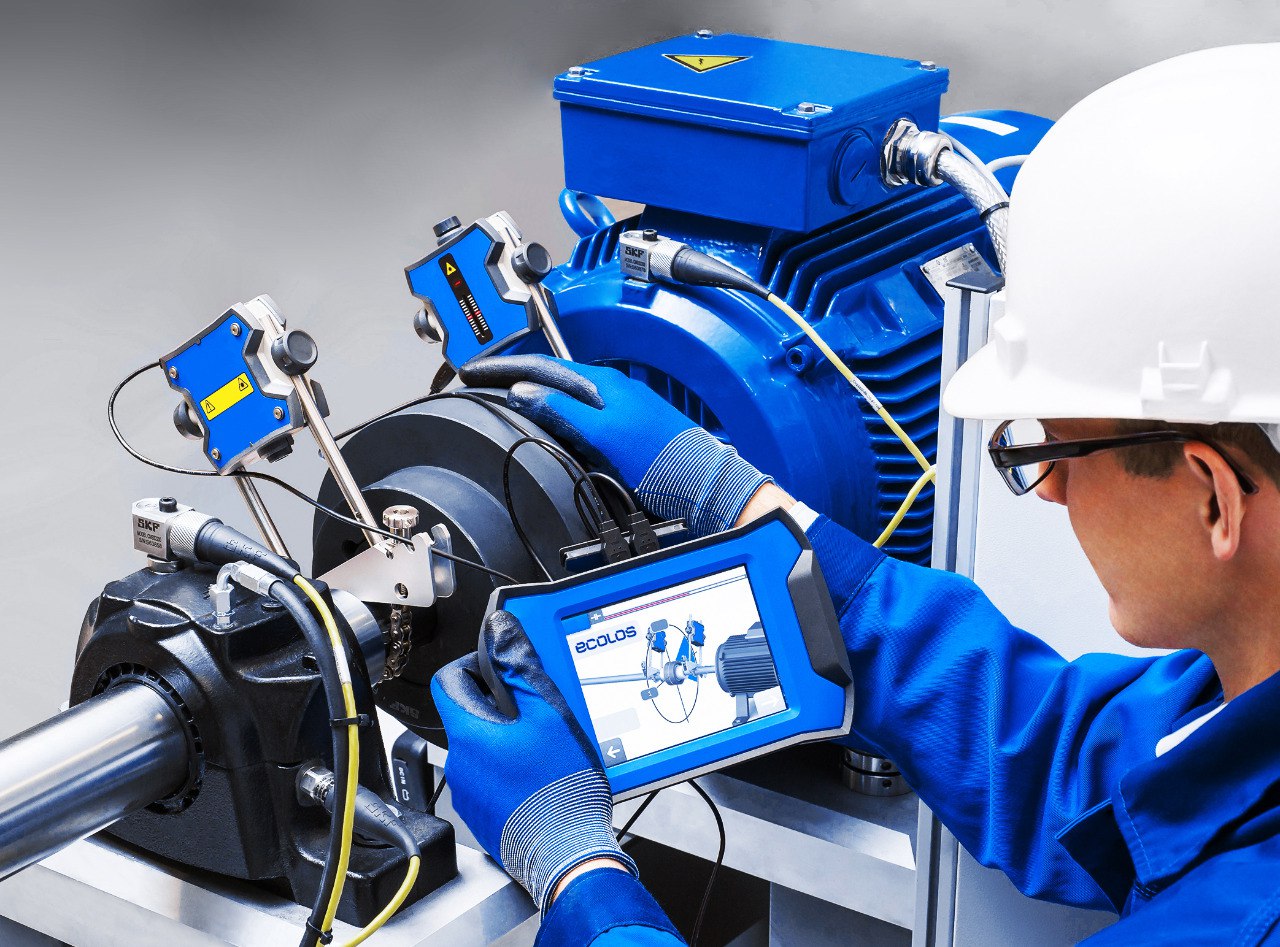
Основные цели испытаний узлов и агрегатов
- Проверка на надёжность: тестирование на устойчивость к нагрузкам и экстремальным условиям.
- Обнаружение дефектов: выявление производственных или проектных недоработок.
- Соблюдение стандартов и нормативов: соответствие отраслевым требованиям безопасности и качества.
- Оценка долговечности: прогнозирование срока службы устройства на основании испытаний.
Виды испытаний и их преимущества
1. Функциональные испытания
Проверка базовых функций оборудования для подтверждения его работоспособности.
- Преимущества: выявление ошибок в программных и механических компонентах до начала эксплуатации.
- Особенности: применяются как для отдельных узлов, так и для готовых систем.
2. Статические и динамические испытания
Статические испытания проверяют устойчивость к неподвижным нагрузкам, в то время как динамические тесты исследуют поведение компонентов в движении или под нагрузкой.
- Преимущества: статические тесты выявляют критические зоны в конструкции, а динамические испытания помогают предсказать износ.
- Особенности: используются для компонентов, подверженных высоким нагрузкам, таких как двигатели, трансмиссии и другие механизмы.
3. Климатические и температурные испытания
Такие тесты определяют, как оборудование работает при экстремальных температурах, влажности, вибрации и других климатических воздействиях.
- Преимущества: проверка устойчивости материалов и конструкций в неблагоприятных условиях.
- Особенности: критически важны для изделий, работающих в экстремальных условиях (например, нефтегазовое и космическое оборудование).
4. Испытания на усталость и износ
Проводятся для определения долговечности компонентов и способности выдерживать многократные нагрузки.
- Преимущества: позволяют спрогнозировать возможные поломки и продлить срок эксплуатации оборудования.
- Особенности: применяются для деталей, подверженных постоянному трению или вибрации.
Основные этапы испытаний
1. Подготовка к испытаниям
- Составление плана испытаний: определение типов и условий тестирования.
- Подготовка оборудования и инструментов: настройка оборудования для тестов.
- Анализ контрольных параметров: фиксация базовых параметров для сравнения с итоговыми результатами.
2. Проведение испытаний
- Испытание отдельных узлов: проверка ключевых компонентов отдельно от всей системы.
- Тестирование сборки: комплексная проверка всех узлов в составе устройства для оценки взаимодействия компонентов.
- Измерение параметров и сбор данных: фиксация данных для анализа результатов.
3. Анализ результатов
- Сравнение с нормативами: оценка соответствия параметров оборудования стандартам.
- Выявление проблемных зон: анализ слабых мест конструкции.
- Корректировка документации: обновление чертежей, спецификаций и рекомендаций по эксплуатации.
Преимущества тестирования узлов и агрегатов
- Снижение затрат на ремонт: раннее выявление дефектов минимизирует затраты на устранение неполадок.
- Продление срока службы оборудования: улучшенные материалы и технологии уменьшают вероятность поломок.
- Соблюдение требований безопасности: тестирование помогает избежать аварий и повысить безопасность эксплуатации.
- Повышение качества продукции: оптимизация конструкции на основе результатов испытаний.
Заключение
Испытания узлов и агрегатов — неотъемлемая часть обеспечения надёжности оборудования. Эти тесты помогают снизить риски, продлить срок службы устройств и обеспечить их соответствие высоким стандартам качества и безопасности. Регулярное тестирование и анализ результатов позволяют производителям оперативно вносить улучшения в конструкцию и материалы, создавая конкурентоспособные и долговечные продукты.